Breakdown maintenance adalah salah satu pendekatan pemeliharaan yang sering kali dianggap sebagai opsi terakhir dalam manajemen aset industri. Berbeda dengan metode pemeliharaan lainnya, metode ini berfokus pada perbaikan setelah terjadi kegagalan atau kerusakan peralatan.
Artikel ini akan membahas secara mendalam tentang apa itu breakdown maintenance, jenis-jenis yang biasa diterapkan, serta strategi yang efektif untuk mengelola dan meminimalkan dampaknya. Dengan memahami konsep dan penerapan pemeliharaan ini, perusahaan dapat mengembangkan rencana pemeliharaan yang lebih komprehensif dan responsif, yang pada akhirnya meningkatkan efisiensi operasional dan memperpanjang umur aset.
Table of Contents
ToggleApa Itu Breakdown Maintenance?
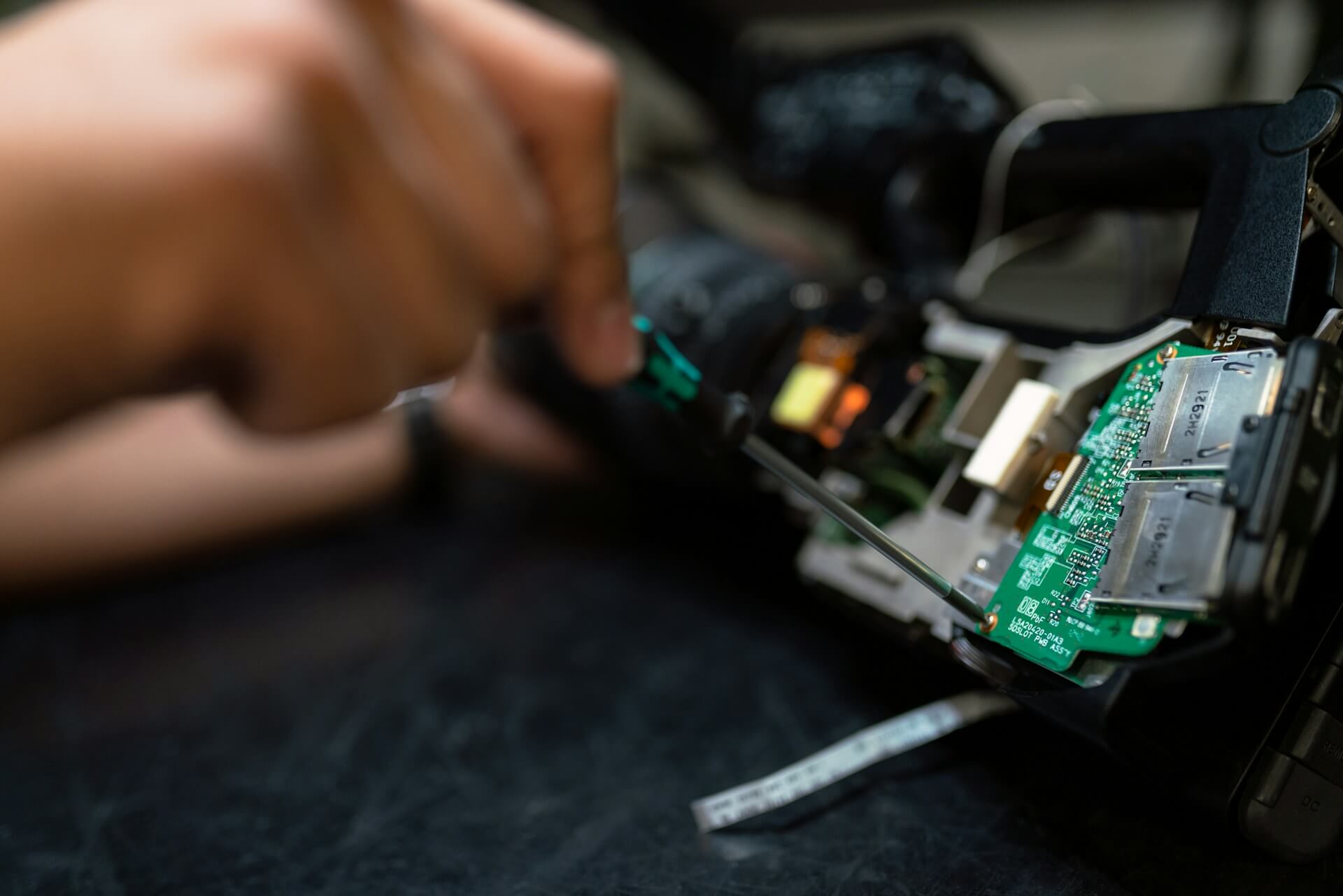
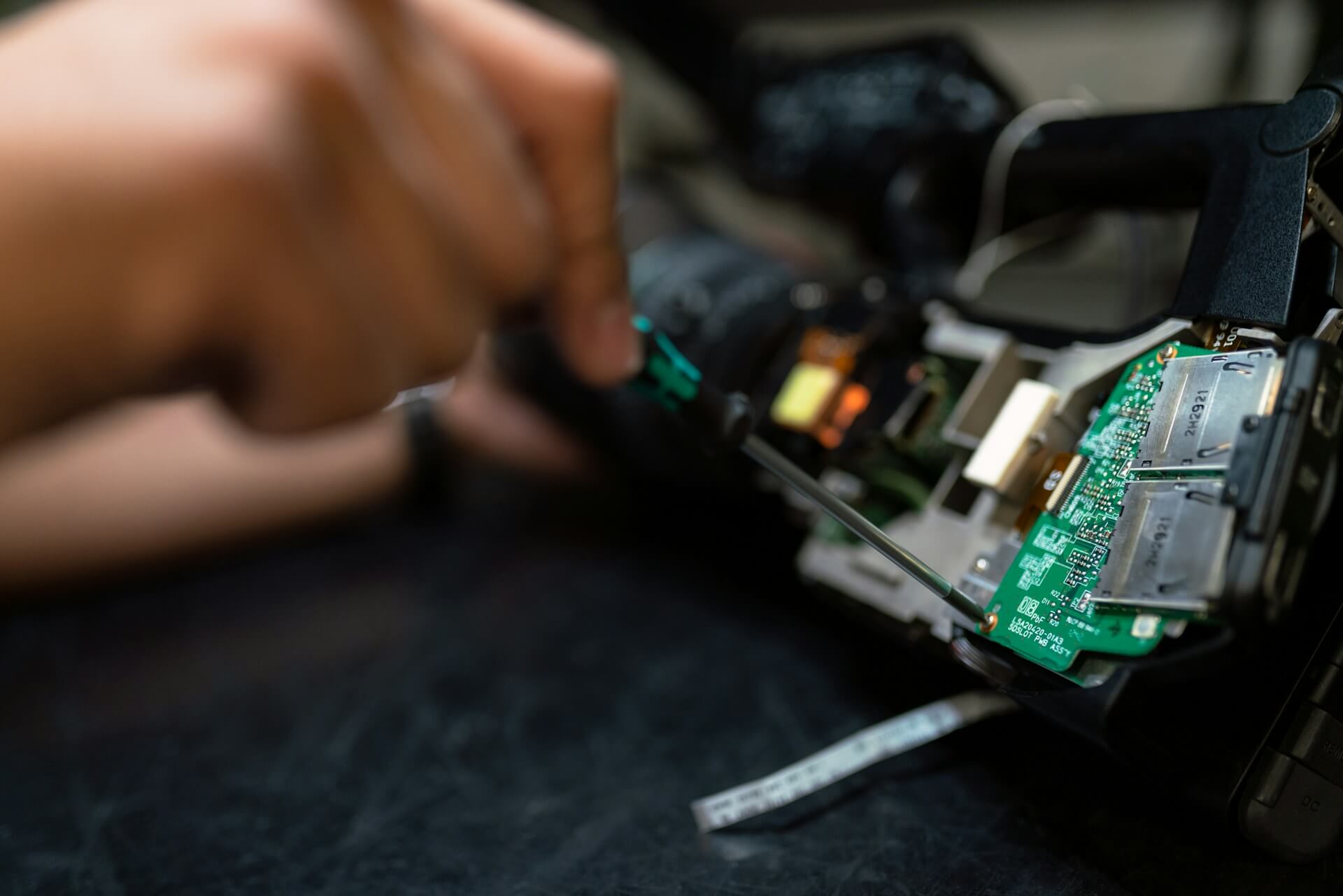
Breakdown maintenance adalah strategi pemeliharaan di mana perbaikan dilakukan hanya setelah peralatan mengalami kerusakan atau kegagalan total. Metode ini tidak melibatkan tindakan pencegahan, melainkan menunggu hingga peralatan berhenti berfungsi sebelum memperbaikinya.
Walaupun sering dianggap kurang efisien karena bisa menyebabkan downtime yang tidak terduga, breakdown maintenance dapat menjadi pilihan praktis untuk peralatan yang tidak kritis atau memiliki biaya perbaikan yang rendah. Fokus utama dari pendekatan ini adalah memperbaiki peralatan secepat mungkin untuk meminimalkan gangguan operasional dan memastikan kembali berfungsinya sistem dengan segera.
Jenis-jenis Breakdown Maintenance
Breakdown maintenance dapat dibagi menjadi beberapa jenis berdasarkan kondisi dan penyebab kerusakan peralatan. Berikut adalah penjelasan mengenai masing-masing jenisnya:
1. Corrective Breakdown Maintenance
Corrective breakdown maintenance adalah jenis pemeliharaan yang dilakukan setelah peralatan mengalami kegagalan atau kerusakan. Tujuannya adalah untuk memperbaiki masalah dan mengembalikan peralatan ke kondisi operasional secepat mungkin.
Pendekatan ini sering diterapkan ketika kerusakan tidak dapat diprediksi atau jika biaya perawatan preventif dianggap lebih tinggi daripada biaya perbaikan setelah kerusakan terjadi. Contohnya adalah perbaikan mesin produksi yang tiba-tiba berhenti beroperasi karena komponen internal yang aus atau rusak.
2. Run-to-Failure Maintenance
Run-to-failure maintenance adalah strategi di mana peralatan dibiarkan beroperasi sampai terjadi kegagalan total, tanpa intervensi pemeliharaan preventif. Strategi ini cocok untuk peralatan non-kritikal atau peralatan yang biaya perbaikannya relatif rendah dan tidak akan menyebabkan dampak besar pada operasi jika rusak. Contoh peralatan yang sering kali menggunakan pendekatan ini adalah lampu penerangan, kipas angin, atau peralatan kantor yang tidak esensial.
3. Deferred Maintenance
Deferred maintenance adalah situasi di mana pemeliharaan ditunda atau dijadwalkan ulang hingga waktu yang lebih sesuai, sering kali karena keterbatasan sumber daya atau prioritas operasional lainnya. Meskipun dapat menyebabkan risiko peningkatan kerusakan, jenis pemeliharaan ini sering kali diterapkan dalam situasi di mana kerusakan tidak segera mempengaruhi operasi secara signifikan.Misalnya, perbaikan minor pada mesin produksi yang dijadwalkan ulang hingga akhir pekan untuk menghindari gangguan produksi.
4. Emergency Maintenance
Emergency maintenance adalah tindakan pemeliharaan yang dilakukan segera setelah peralatan mengalami kegagalan kritis yang mengganggu operasi secara signifikan. Perbaikan dilakukan secepat mungkin untuk mengembalikan fungsi peralatan dan meminimalkan downtime. Jenis pemeliharaan ini membutuhkan respons cepat dan sering kali melibatkan biaya tinggi karena urgensi dan kebutuhan akan sumber daya yang cepat. Contohnya adalah perbaikan sistem pendingin dalam pabrik pengolahan makanan yang rusak dan mengancam kualitas produk.
Proses Breakdown Maintenance
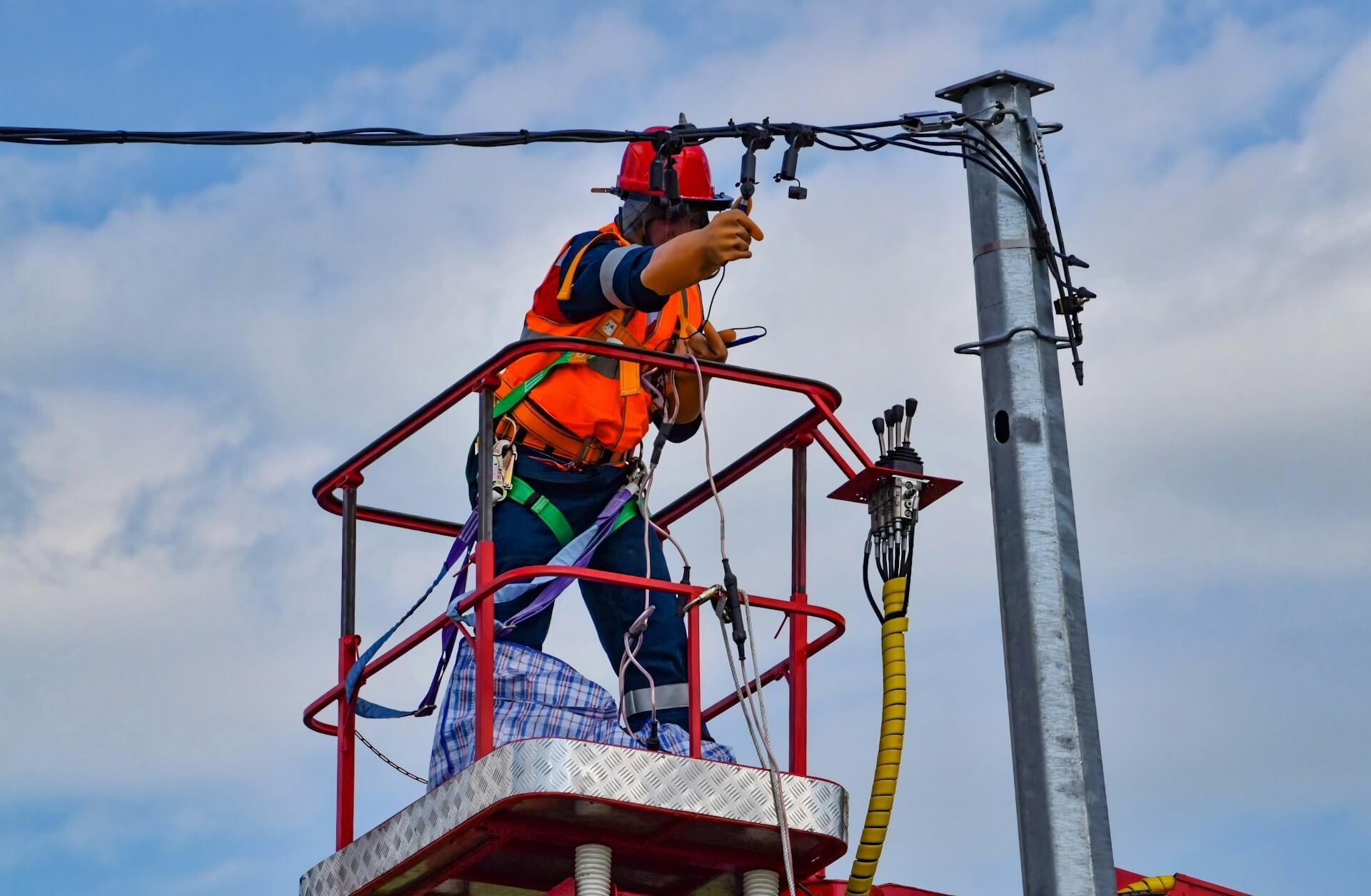
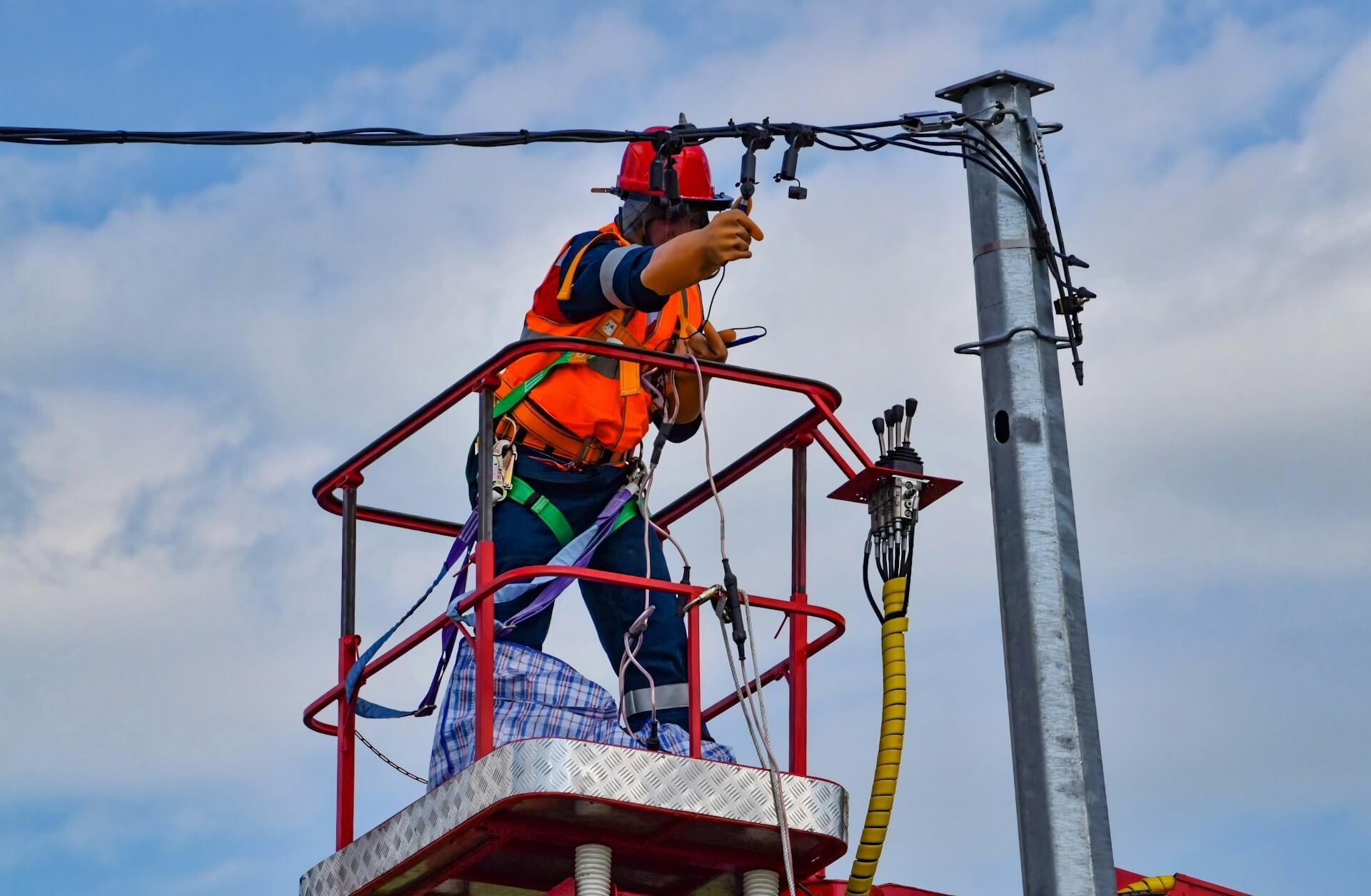
Breakdown maintenance adalah pendekatan pemeliharaan yang diaktifkan setelah terjadi kegagalan atau kerusakan pada peralatan. Proses ini melibatkan beberapa tahapan utama, yaitu:
1. Identifikasi Kegagalan
Langkah pertama dalam proses breakdown maintenance adalah mengidentifikasi bahwa kerusakan atau kegagalan telah terjadi. Ini bisa melalui laporan dari operator, sistem pemantauan otomatis, atau inspeksi visual. Identifikasi yang cepat dan akurat sangat penting untuk meminimalkan dampak kerusakan pada operasi.
2. Penilaian Kerusakan
Setelah kegagalan diidentifikasi, langkah berikutnya adalah menilai tingkat kerusakan. Teknisi atau tim pemeliharaan harus menentukan penyebab kerusakan, bagian yang terpengaruh, dan dampak keseluruhan terhadap sistem. Penilaian ini membantu dalam merencanakan tindakan perbaikan yang tepat dan memastikan semua aspek kerusakan diperhitungkan.
3. Perencanaan dan Persiapan Perbaikan
Berdasarkan penilaian kerusakan, langkah selanjutnya adalah merencanakan perbaikan. Ini melibatkan pengumpulan alat dan suku cadang yang diperlukan, serta menentukan urutan pekerjaan yang harus dilakukan. Persiapan yang baik dapat mempercepat proses perbaikan dan mengurangi downtime.
4. Pelaksanaan Perbaikan
Tahap ini melibatkan pelaksanaan tindakan perbaikan sesuai dengan rencana yang telah disusun. Teknisi akan mengganti atau memperbaiki komponen yang rusak, melakukan pengujian untuk memastikan perbaikan berhasil, dan memastikan bahwa peralatan dapat berfungsi kembali dengan baik. Proses ini harus dilakukan dengan cermat untuk menghindari kesalahan yang bisa memperpanjang waktu perbaikan.
5. Pengujian dan Verifikasi
Setelah perbaikan selesai, peralatan harus diuji untuk memastikan bahwa semua masalah telah diatasi dan peralatan berfungsi sesuai spesifikasi. Pengujian ini melibatkan pengoperasian peralatan dalam kondisi normal dan memantau kinerjanya untuk memastikan bahwa tidak ada masalah yang tersisa.
Keuntungan dan Kekurangan Breakdown Maintenance
Breakdown maintenance memiliki sejumlah keuntungan dan kekurangan yang perlu dipertimbangkan dalam manajemen pemeliharaan peralatan. Berikut adalah penjelasan mendetail mengenai keuntungan dan kekurangan dari pendekatan ini:
Keuntungan
1. Sederhana dan Mudah Diterapkan
Breakdown maintenance adalah pendekatan yang relatif sederhana dan mudah diterapkan. Karena pemeliharaan hanya dilakukan setelah peralatan mengalami kerusakan, tidak diperlukan jadwal pemeliharaan yang kompleks atau sumber daya yang besar untuk tindakan preventif.
2. Biaya Awal Rendah
Dengan tidak adanya kebutuhan untuk pemeliharaan rutin dan preventif, biaya awal yang diperlukan untuk menerapkan pendekatan ini cenderung lebih rendah. Perusahaan tidak perlu mengeluarkan biaya untuk inspeksi rutin, pelumasan, atau penggantian suku cadang secara periodik.
3. Penggunaan Maksimal Peralatan
Pendekatan ini memungkinkan penggunaan peralatan hingga batas maksimal sebelum memerlukan perbaikan. Ini berarti setiap komponen digunakan sepenuhnya, yang dapat mengurangi pemborosan suku cadang yang masih layak pakai.
4. Minimalkan Gangguan Tidak Diperlukan
Karena tidak ada pemeliharaan preventif yang dijadwalkan secara rutin, gangguan operasional yang disebabkan oleh pemeliharaan yang tidak perlu dapat diminimalkan. Ini bisa sangat menguntungkan dalam lingkungan produksi yang membutuhkan operasi terus-menerus.
Kekurangan
1. Downtime Tak Terduga
Salah satu kekurangan terbesar dari breakdown maintenance adalah risiko downtime yang tidak terduga. Ketika peralatan tiba-tiba rusak, operasi bisa terhenti, yang dapat menyebabkan penundaan produksi dan hilangnya pendapatan.
2. Biaya Perbaikan Tinggi
Kerusakan mendadak sering kali memerlukan perbaikan darurat yang bisa lebih mahal dibandingkan dengan pemeliharaan preventif. Biaya tambahan ini bisa mencakup biaya tenaga kerja darurat, pengiriman cepat suku cadang, dan layanan teknisi spesialis.
3. Kerusakan Berantai
Ketika satu komponen rusak, kerusakan tersebut bisa menyebabkan masalah pada komponen lain yang berhubungan. Hal ini bisa meningkatkan kompleksitas dan biaya perbaikan, serta memperpanjang waktu yang dibutuhkan untuk mengembalikan peralatan ke kondisi operasional.
4. Penurunan Umur Peralatan
Tanpa pemeliharaan preventif, peralatan mungkin lebih sering mengalami kerusakan yang bisa memperpendek umur operasionalnya. Pemeliharaan yang tidak dilakukan secara berkala dapat menyebabkan komponen bekerja di luar spesifikasi optimal, yang pada akhirnya mempercepat keausan dan kerusakan.
Strategi untuk Mengoptimalkan Breakdown Maintenance
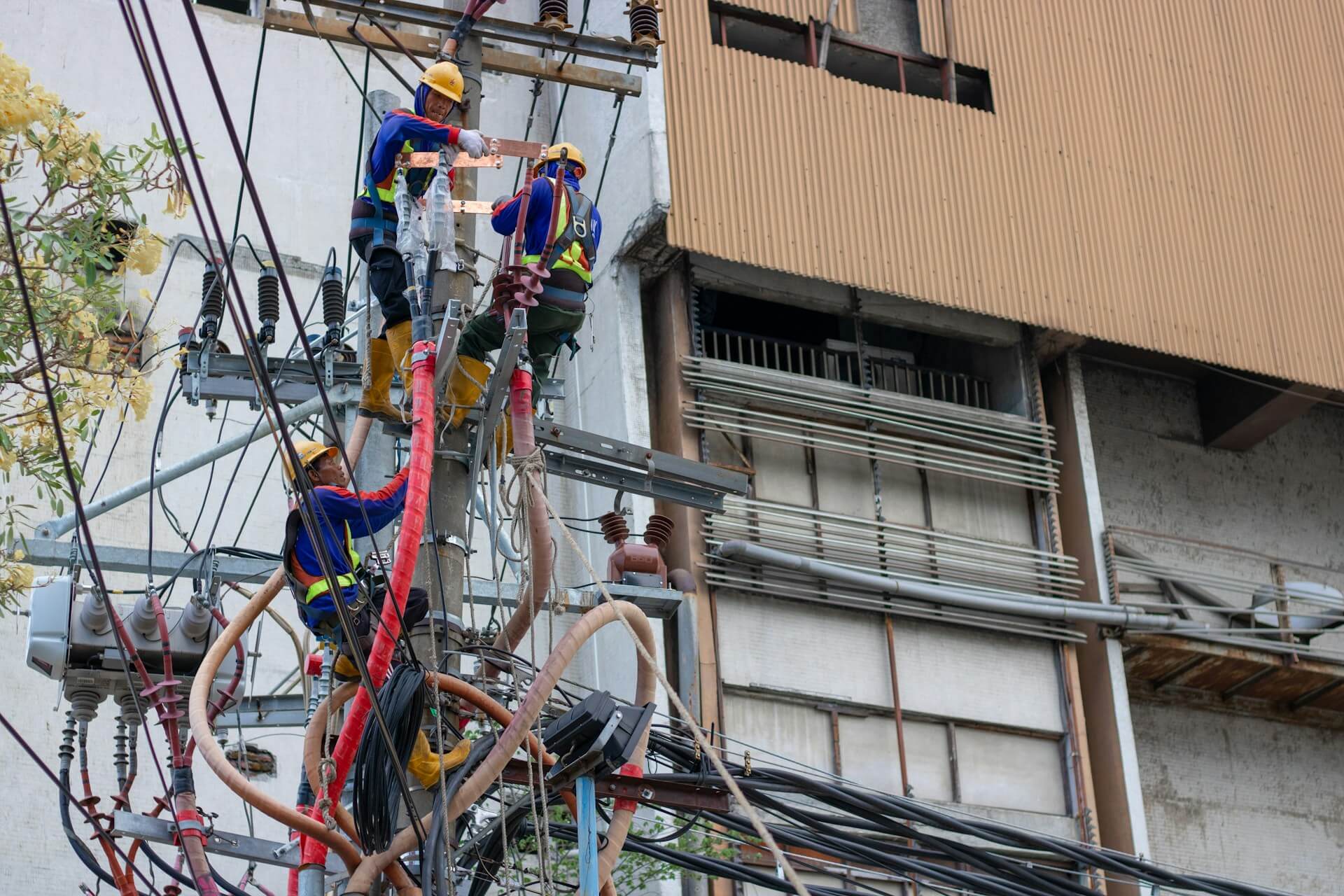
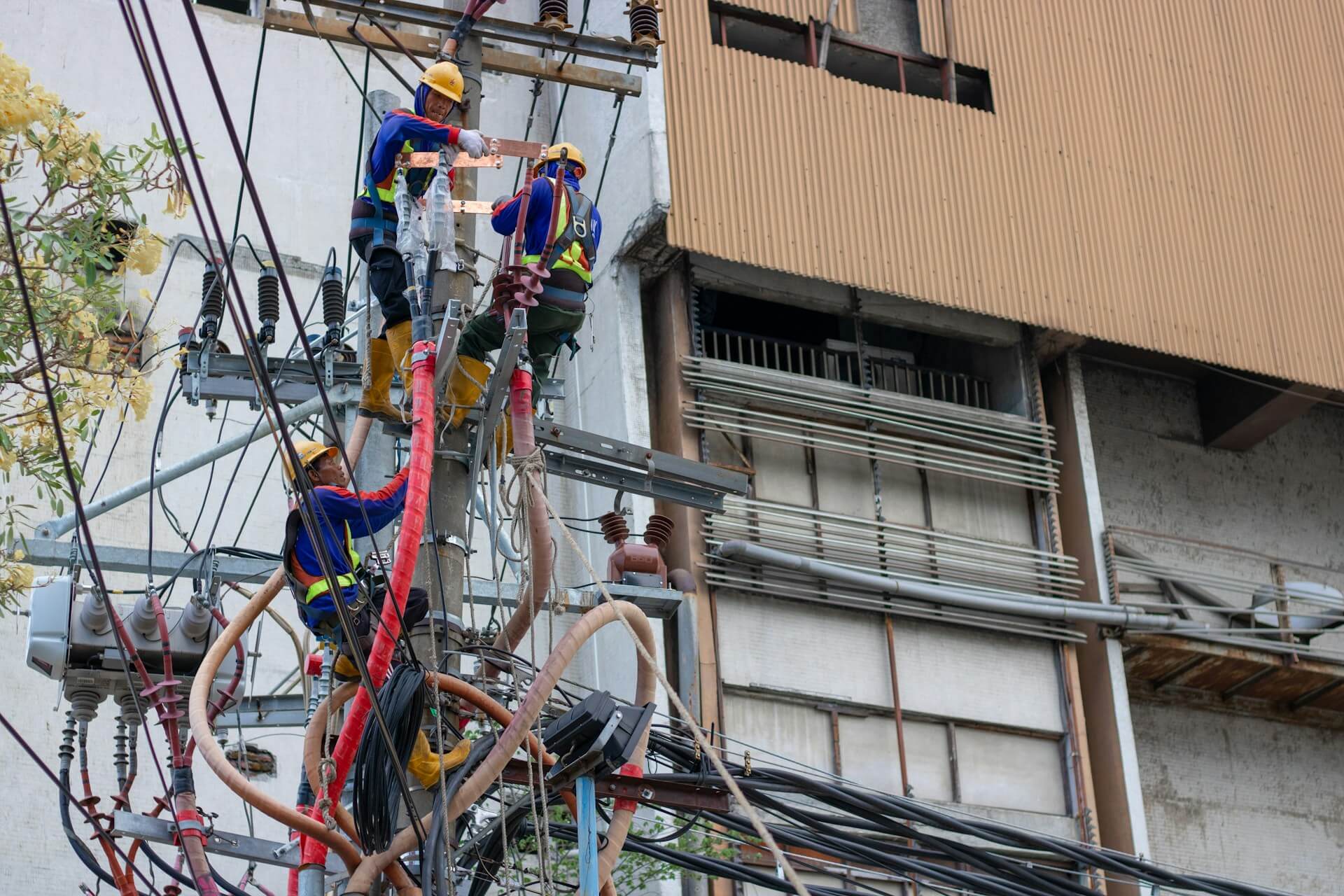
Mengoptimalkan breakdown maintenance memerlukan pendekatan yang terstruktur dan strategi yang tepat untuk meminimalkan dampak negatif dan meningkatkan efisiensi operasional. Berikut adalah beberapa strategi yang dapat diterapkan:
1. Peningkatan Sistem Monitoring
Menggunakan sistem pemantauan yang canggih dapat membantu dalam mendeteksi tanda-tanda awal kerusakan sebelum peralatan benar-benar gagal. Sensor dan teknologi Internet of Things (IoT) memungkinkan pemantauan kondisi peralatan secara real-time, sehingga tindakan perbaikan dapat dilakukan segera setelah masalah terdeteksi.
2. Pelatihan dan Keterampilan Teknisi
Memastikan teknisi memiliki keterampilan dan pengetahuan yang memadai untuk menangani perbaikan peralatan adalah kunci dalam breakdown maintenance. Pelatihan rutin dan sertifikasi dapat membantu teknisi menjadi lebih efektif dan efisien dalam mendiagnosis dan memperbaiki kerusakan.
3. Pengelolaan Suku Cadang
Menjaga inventaris suku cadang yang memadai adalah penting untuk meminimalkan waktu tunggu saat peralatan rusak. Melakukan analisis untuk menentukan suku cadang yang paling sering dibutuhkan dan memastikan ketersediaannya dapat mempercepat proses perbaikan.
4. Analisis Akar Penyebab (Root Cause Analysis)
Setiap kali terjadi kerusakan, melakukan analisis akar penyebab dapat membantu mengidentifikasi sumber masalah. Dengan memahami penyebab utama kerusakan, tindakan pencegahan yang lebih efektif dapat diimplementasikan untuk mencegah kejadian serupa di masa depan.
5. Pemeliharaan Terencana
Meskipun fokusnya pada breakdown maintenance, mengintegrasikan elemen pemeliharaan terencana dapat membantu. Misalnya, melakukan inspeksi visual dan pembersihan rutin dapat mengidentifikasi potensi masalah sebelum mereka menjadi kegagalan yang signifikan.
Kesimpulan
Breakdown maintenance adalah pendekatan pemeliharaan yang dilakukan setelah peralatan mengalami kegagalan. Meskipun sederhana dan biaya awal rendah, metode ini memiliki risiko downtime tak terduga dan biaya perbaikan tinggi.
Strategi optimalisasi mencakup peningkatan sistem monitoring, pelatihan teknisi, pengelolaan suku cadang, analisis akar penyebab, dan penggunaan data analitik. Dengan pendekatan yang tepat, breakdown maintenance dapat dikelola lebih efektif, mengurangi dampak negatif, dan meningkatkan efisiensi operasional perusahaan.